13 මාර් PCB කර්මාන්තයේ ඉහළම ඵලදායිතා ඝාතකයන් පස්දෙනා
සමහර විසඳුම්
කර්මාන්තශාලා බිම්වල ඵලදායිතාව උපරිම කිරීම සඳහා මාර්ගය පිහිටා ඇත්තේ පෙර කොටස්වල සවිස්තරාත්මක මෙහෙයුම් කරුණු ආමන්ත්රණය කරන ඉහළ-පහළ ප්රවේශයකිනි. පහත සඳහන් ක්ෂේත්රවල පියවර ගත යුතුය: දත්ත සැකසීම නිෂ්පාදන ක්රියාවලි අනුකරණය නිෂ්පාදන ක්රියාවලි සකස් කිරීම නිෂ්පාදන ක්රියාත්මක කිරීමේ පද්ධති මෙම සියලු අභියෝග සඳහා තාක්ෂණික විසඳුම් අවශ්ය වේ. තවද, තීරණාත්මක ලෙස, කාර්ය සාධනය වැඩි දියුණු කිරීම සඳහා ගත යුතු නිශ්චිත ක්රියාමාර්ග හඳුනා ගන්නා ඉංජිනේරුවන්, රේඛීය ක්රියාකරුවන් සහ නිෂ්පාදන කළමනාකරුවන් සඳහා වාර්තාකරණ පද්ධති ක්රියාත්මක විය යුතුය. එපමනක් නොව, අවස්ථාව අහිමි වීමට පෙර සහ වෙනත් තැන්වල නැවුම් ගැටළු මතු වීමට පෙර වැඩිදියුණු කිරීම් සිදු කිරීමට හැකි වන පරිදි තොරතුරු කාලෝචිත විය යුතුය. දත්ත සැකසීම සංරචක ආකෘති ආදානය සහ සැලසුම් දත්ත ආදානය යන දෙකටම දත්ත සැකසීම කෙරෙහි අවධානය යොමු කිරීම අනිවාර්ය පළමු පියවරකි: සංරචක ආකෘති නිර්මාණය - නිෂ්පාදකයින් විසින් පෑස්සුම් සඳහා සම්බන්ධතා සම්බන්ධතා ඇතුළුව රේඛාවේ භාවිතා කිරීමට අදහස් කරන සියලුම කොටස්වල නිවැරදි භෞතික ආකෘති නිර්මාණය කළ යුතුය. සන්ධි, CAD දත්ත සමඟ ඒකාබද්ධ වේ. මෙය සමන්විත විය යුතුය: ස්ථාවර, CAD-පුස්තකාල මධ්යස්ථ, ප්රමිතිගත DFM සහ ක්රියාවලි සැකසීමේ ක්රියාකාරකම් පහළට සක්රීය කිරීම සඳහා කොටස් ආකෘතිකරණය. සාමාන්යකරණය කරන ලද සංරචක ඕෆ්-සෙට්, භ්රමණ සහ ධ්රැවීයතා ප්රකාශ ප්රමිතියකට. ලොව පුරා ඉලෙක්ට්රොනික කර්මාන්තයේ විකුණුම් ඩොලර් බිලියන 750 ක් වන අතර එයින් තුනෙන් දෙකක් PCB එකලස් කිරීම මගින් සිදු කෙරේ. PCB නිෂ්පාදනය සැලකිය යුතු කර්මාන්ත රියදුරන් තිදෙනෙකුගේ සන්දර්භය තුළ ඵලදායිතාව වැඩි කිරීම සඳහා වන උමතු තල්ලුවක් මගින් සංලක්ෂිත වේ: කෙටි නිෂ්පාදන ජීවන චක්ර - වඩා හොඳ නිෂ්පාදන සංවර්ධනය කිරීම සහ තරඟයට පෙර වෙළඳපොළට ගෙන ඒම සඳහා පීඩනය යෙදී ඇත, අඩු වියදමකින්, සමගාමීව සංවර්ධනය කිරීම. ඊළඟ පරම්පරාවේ නිෂ්පාදනයක්. වසර පහකට පෙර, නිෂ්පාදන ජීවන චක්ර මනිනු ලැබුවේ වසර වලින්; දැන් ඒවා මාස වලින් මනිනු ලබන අතර, මූලාකෘති අවධියේ සිට ඉහළ පරිමාවකින් යුත් නිෂ්පාදනය දක්වා ගමන් කිරීමේ ක්රියාවලිය වේගවත් කිරීම සඳහා නිර්මාණකරුවන් සහ නිෂ්පාදකයින් මත පීඩනයක් ඇති කරයි. වඩාත් සංකීර්ණත්වය - නිෂ්පාදකයින් විසින් වැඩි කරන ලද කුඩාකරණය සහ වඩාත් සංකීර්ණ පුවරු සමඟ වඩාත් සංකීර්ණ, ඉහළ ඝනත්ව මෝස්තර නිෂ්පාදනය කරයි. PCB එකලස් කිරීමක් සඳහා සාමාන්ය ද්රව්ය බිල්පතකට (BOM) දැන් අනන්ය රේඛීය අයිතම සිය ගණනකින් සෑදූ සම්පූර්ණ කොටස් දහස් ගණනක් තිබිය හැක. "මිලදී ගත්" අයිතම - ධාරිත්රක, ප්රතිරෝධක, ඩයෝඩ සහ යනාදිය - අවම BOM පිරිවැය සහ උපරිම කොටස් ලබා ගැනීමේ හැකියාව සක්රීය කිරීම සඳහා එක් එක් "විකල්ප කොටස්" එකක් හෝ කිහිපයක් ඇත. වඩාත් සංකීර්ණ ද්රව්ය බිල්පත් (BOM) සංරචකයේ ගුණාත්මක භාවය වැඩි කිරීම සහ වඩා හොඳ සොයා ගැනීමේ හැකියාව මත වාරිකයක් ලබා දෙයි. බාහිරින් ලබා ගැනීම වේගයෙන් වර්ධනය වේ - කෙටි නිෂ්පාදන ජීවන චක්ර සහ වැඩි වූ සංකීර්ණත්වය OEM වලට බාහිරින් ලබා ගැනීම වැළඳ ගැනීමට බල කර ඇත, දැන් PCB කර්මාන්තයේ වේගයෙන්ම වර්ධනය වන අංශය වේ. ඉලෙක්ට්රොනික් නිෂ්පාදන සේවා (ඊඑම්එස්) සමාගම් 21 දී වෙළඳපොලෙන් 2004% ක් හිමිකර ගත් නමුත් 30 වන විට ඔවුන්ගේ කොටස 2008% දක්වා ළඟා වනු ඇත. එම කාලය තුළ සමස්ත වෙළඳපල වර්ධනය වනු ඇත්තේ 16% ක් පමණි. EMS සපයන්නන් අඩු මිල ගණන්, වේගවත්-වෙළඳපොළට-වෙළඳපොළට සහ වඩා හොඳ ඇණවුම ඉටුකිරීමේ කාර්ය සාධනය පිරිනමන්නේ ඔවුන් විවිධ පාරිභෝගිකයින් සිය ගණනකට සේවා සැපයීමෙන් ලබාගත් දැවැන්ත සමූහ මිලදී ගැනීමේ ශක්තිය සහ ඔවුන්ගේ නිෂ්පාදන වත්කම් ඒකාබද්ධ කිරීම සහ අවම ඒකක පිරිවැයක් ළඟා කර ගැනීමට ඒවා කළමනාකරණය කිරීම නිසාය. EMS සපයන්නන් නිෂ්පාදන සහ සංරචක ප්රසම්පාදනය පිළිබඳ ඔවුන්ගේ මූලික නිපුණතාවය කෙරෙහි අවධානය යොමු කරයි; නව නිෂ්පාදන සැලසුම් කිරීම සහ අලෙවි කිරීම කෙරෙහි අවධානය යොමු කිරීමට OEMs නිදහස් වේ. මෙම කර්මාන්ත ප්රවණතා හොඳින් වටහාගෙන ඇති අතර PCB එකලස් කිරීම ලෝකයේ වඩාත්ම තරඟකාරී කර්මාන්ත වලින් එකක් බවට පත් කිරීමට දායක වී ඇත. පිරිවැය කපා හැරීමට පීඩනයක් ඇතිව, සමගාමීව අස්වැන්න සහ වෙළඳපොළට වේගය වැඩි දියුණු කරන අතරම, තරඟකාරිත්වය වැඩිදියුණු කළ හැකි කර්මාන්තශාලා මහලේ මෙහෙයුම් සඳහා එම වෙනස්කම් සඳහා සෙවීම ආරම්භ වේ. සාමාන්යයෙන්, PCB එකලස් කිරීමේ මෙහෙයුම්වල ආයෝජනය කරන ලද ස්ථාවර වත්කම් ප්රාග්ධනයෙන් 60-70% ක් එකලස් කිරීමේ රේඛාවල ඇති යන්ත්රවල අගුලු දමා ඇත. SMT එකලස් කිරීම විශේෂයෙන් ප්රාග්ධන තීව්ර වේ, නිදසුනක් ලෙස, තනි රේඛාවක් ඩොලර් මිලියනයකට වඩා වැඩි වන අතර මිල වැඩි වේ. දැඩි පීඩනයකට ලක් වූ නිෂ්පාදන කම්හල් කළමනාකරුවන් තම ආයෝජනය කළ ප්රාග්ධනය උපරිම ඵලදායිතාව සහ තරඟකාරිත්වය ලබා දෙන බව සහතික කරන්නේ කෙසේදැයි තමන්ගෙන්ම විමසා සිටිති. පිළිතුර තනි යන්ත්ර මට්ටමින් පමණක් නොව, සම්පූර්ණ රේඛාවේ හෝ කර්මාන්තශාලා මහලේ මට්ටමේ ද පවතී. PCB එකලස් කරන්නන් නිෂ්පාදන කාර්ය සාධනය පිළිබඳ බොහෝ මිනුම් භාවිතා කරයි චක්ර-කාලය, රේඛීය බීට්-අනුපාත සහ පළමු-පාස් අස්වැන්න යන නිෂ්පාදන අතුරු නිෂ්පාදන විශේෂතා, "BOM පරිවර්තන පිරිවැය" සහ ප්රාග්ධනය මත ප්රතිලාභ වැනි ඉහළ මට්ටමේ මිණුම් සලකුණු දක්වා. කුමන ප්රධාන කාර්ය සාධන දර්ශක (KPIs) භාවිතා කළත්, ඉලක්කය වන්නේ පවතින එකලස් කිරීමේ මාර්ග, ද්රව්ය, සවිකෘත සහ මානව සම්පත් වලින් පිළිගත හැකි ගුණාත්මක නිෂ්පාදනයේ උපරිම නිමැවුම උත්පාදනය කිරීමයි.
- කොටස් අවුල්
- අකාර්යක්ෂම රේඛාවක් සැකසීම
- ප්රශස්ත ස්පන්දන අනුපාතවලට වඩා සෙමින්
- අඩු යන්ත්ර උපරිම ක්රියාකාරිත්වය
- PCB/ක්රියාවලි සංයෝජනය උප-ප්රශස්ත වේ
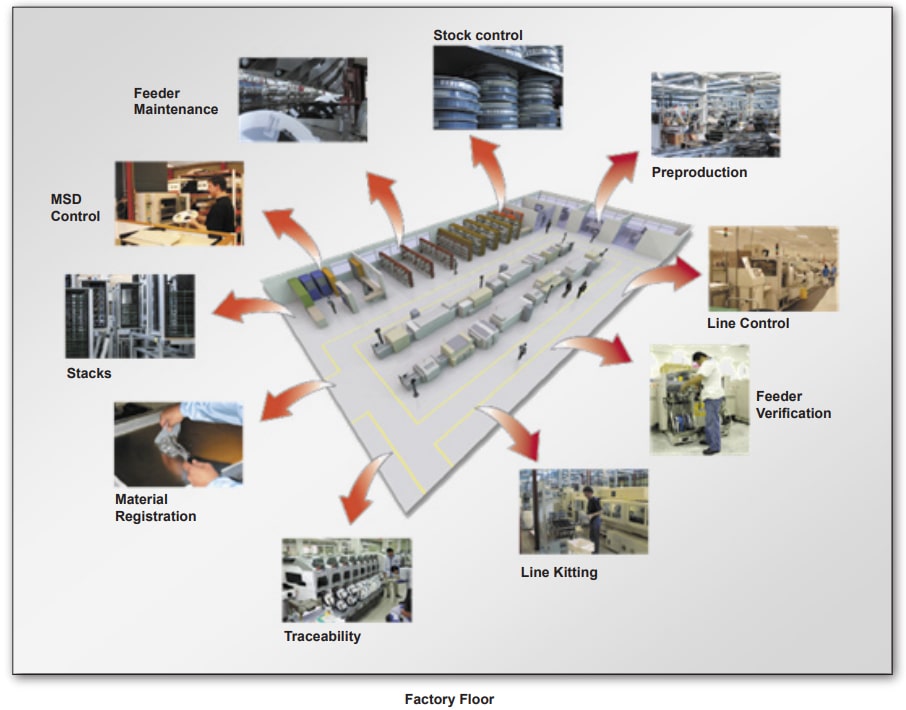
- කොටස් ව්යාකූලත්වය ඵලදායිතාවයට බලපාන පළමු ගැටළුව නම්, ද්රව්ය නියමිත වේලාවට නියමිත ස්ථානයේ නොතිබීම, එකලස් කිරීමේ මාර්ගවල භාවිතයට සූදානම් වීමයි. බොහෝ දෙනා විශ්වාස කරන්නේ ERP හෝ සියලුම BOM වල ප්රධාන කොටස් පාලන පද්ධතිය තුළ සම්පූර්ණ ආවරණයක් තිබීම ප්රමාණවත් බවයි. නමුත් තීරණාත්මක සාධකය වන්නේ යන්ත්රවල අවශ්ය වේලාවට නියමිත වේලාවට කොටස් සහ ද්රව්යවල නිවැරදි ප්රමාණයන් තිබීම සහ යන්ත්රවල ස්ථාපනය කිරීමයි. සංරචක කොටස් අංක තොග වශයෙන් තිබේද යන්න තහවුරු කිරීම කර්මාන්තශාලා මහලේ කොටස් නොමැති වීම හේතුවෙන් නිෂ්පාදනය අසාර්ථක වීම වැළැක්විය නොහැක.
i. වෙනත් සැකසුම් සඳහා දැනටමත් කැපවී ඇති කොටස් - PCB මත එකලස් කිරීම සඳහා වන සංරචක සාමාන්යයෙන් තොග වශයෙන් හසුරුවනු ලැබේ - එක්කෝ කොටස් දහස් ගණනක් රඳවාගෙන සිටින රීල්වල හෝ සිය ගණනක් රඳවා තබා ගන්නා තැටිවල. නිෂ්පාදන ඇණවුම් දෙකක් සඳහා එකම කොටස් එකවර අවශ්ය නම්, කිසිදු රේඛාවක් නිවැරදිව සැකසිය නොහැක. සාමාන්ය PCB කර්මාන්තශාලා බිමක ඇති සංරචක රීල් හෝ තැටි සිය ගණනක් හරහා මෙම ගැටලුවේ බලපෑම ගුණ කිරීම, සමස්තයක් ලෙස තිබියදීත්, සෑම නිෂ්පාදන ඇණවුමක් සඳහාම නියමිත කොටස් ප්රමාණය රේඛාවලට ලබා දීමට නොහැකි වීමේ අවදානම විශාල කරයි. , නිෂ්පාදන ඇණවුම් සඳහා අවශ්ය සම්පූර්ණ කොටස් ප්රමාණය ප්රධාන කොටස් පාලන පද්ධතියේ මුළු කොටස් ප්රමාණයට ගැලපේ.
ii. ලබා ගත හැකි කොටස් සොයාගත නොහැක - බොහෝ විට, විශාල කර්මාන්තශාලා වල, ERP පද්ධති නිෂ්පාදන තට්ටුවට මුදා හැරීමෙන් පසු ද්රව්ය ඉතා නිවැරදිව නිරීක්ෂණය නොකරයි. ප්රධාන දත්ත - කොටස් වෙන් කර ඇති රේඛාව සම්බන්ධයෙන්, ඔවුන් කැපවී සිටින සැකසුම් තවමත් නිෂ්පාදනයේ තිබේද, සහ එම සැකසුම් තුළ බැඳ ඇති කොටස්වල නියම ප්රමාණය - නිතර අතුරුදහන් වේ. පවතින දත්ත පෙන්නුම් කරන්නේ නිෂ්පාදන ආරම්භ කිරීම සඳහා කොටස් තිබේ නම්, ඒවා නිතර සොයා ගත නොහැක. අනවශ්ය ප්රමාදයන් නිෂ්පාදන ධාවනය ආරම්භයේදී ප්රතිඵලයක් වන අතර “කඩිනම් කරන්නන්” වියරුවෙන් අතුරුදහන් වූ ද්රව්ය සොයමින් සිටී. ඒ හා සමානව, සහ එම කොටස්වල දෘශ්යතාව නොමැතිකම හේතුවෙන්, බොහෝ විට කොටස් අනවශ්ය ලෙස රේඛාවකට ලබා දිය හැකිය, සැකසීමට සහාය වීම, ඇත්ත වශයෙන්ම එම කොටස්වල ප්රමාණවත් සැපයුමක් දැනටමත් රේඛාව මත පටවා ඇති විට, ඉතිරිව ඇත. පෙර නිෂ්පාදන අනුපිළිවෙල. මෙම ලුහුබැඳීමේ සාවද්යතාවයන් කර්මාන්තශාලා බිම් තොගයේ පිරිවැය අනවශ්ය ලෙස වැඩි කිරීමට හේතු වේ. ස්ථානගත කිරීමට පෙර මිස්-පික්ස් හෝ තුණ්ඩ අසමත් වීම හේතුවෙන්. විශාල වශයෙන්, මෙය PCB නිෂ්පාදකයින් අධි තක්සේරු කිරීමට බල කරයි
iii. නිරෝධායනයෙහි ඇති කොටස් - Pick-and-place යන්ත්රයේ අමතර කොටස් ලබා ගැනීමට බලපාන තවත් සාධකයක් වන්නේ කර්මාන්තශාලා බිමෙහි සාමාන්ය වායුගෝලීය තත්ත්වයන්ට නිරාවරණය වීමට සමහර කොටස්වල සංවේදිතාවයි. සමහර විට සංරචක මුද්රා තැබූ බහාලුම් වලින් ඉවත් කිරීමෙන් පසු වායුගෝලීය ආර්ද්රතාවයට බලපාන අතර, පැය කිහිපයකට පසු, සංරචක සිරුරු වලින් තෙතමනය ඉවත් කිරීම සඳහා උඳුනක පිළිස්සිය යුතුය. අවන්-ෙබ්කිං චක්ර මගින් ගෙන එන අනවරතයන් යන්නෙන් අදහස් වන්නේ ඇතැම් කොටස් සෑම විටම “තොගයේ” තිබුණද එකලස් කිරීම සඳහා “ලබා ගත හැකි” සහ “නොලබන” චක්ර හරහා ගමන් කරන බවයි.
iv. සාවද්ය කොටස් පාලනය - ERP පද්ධතිය තුළ පවතින කොටස් තොග ලබා ගැනීමේ හැකියාව වාර්තා නොකළ නාස්තියේ ප්රතිඵලයක් ලෙස නිතර සාවද්ය වේ. කර්මාන්තශාලා බිම භාවිතයෙන් පසු සංරචක ගබඩාවට ආපසු ලබා දෙන විට, රීලයේ කොටස් කීයක් ඉතිරිව තිබේද යන්න පිළිබඳ නිවැරදි චිත්රයක් රැස් කිරීම ගැටළු සහගත වේ. නිෂ්පාදන කළමනාකරුවන් සරලව ආරම්භක ප්රමාණය ගෙන BOM මත අර්ථ දක්වා ඇති ස්ථාන ගණන අඩු කළ යුතුද? බොහෝ විට එසේ නොවේ, මන්ද එය යන්ත්ර තොග මට්ටම් මගින් අහිමි වූ කොටස් නොසලකා හරින අතර, පසුකාලීන නිෂ්පාදන ඇණවුම් වලදී කර්මාන්තශාලා මහලේ අනපේක්ෂිත තොග පිටවීමට හේතු වේ. මෙවැනි මිල අධික (සහ සැලසුම් නොකළ) නිෂ්පාදන වසා දැමීම්, පසුකාලීන ඇණවුම් සඳහා ද්රව්ය ඉවත් කිරීමේ අවශ්යතාවය සහ අඩුපාඩු නිවැරදි කිරීම සඳහා හදිසි කොටස් මිලදී ගැනීම් ඇති කරයි. ERP පද්ධතියේ වාර්තා නිෂ්පාදන තට්ටුවේ යථාර්ථය සමඟ අතින් සමමුහුර්ත කර ඇති අතර, නිෂ්පාදනය අත්යවශ්යයෙන්ම අත්හිටුවා ඇති විට, සාවද්ය කොටස් පාලනය මඟින් වෙබ් අඩවිය පුරා බඩු තොග විගණනය සඳහා කාලය ගතවන සහ මිල අධික භාවිතයට බල කරයි.
v. කොටස් මට්ටම්, පසුකාලීන නිෂ්පාදන ඇණවුම් වලදී කර්මාන්තශාලා මහලේ අනපේක්ෂිත තොග පිටවීම් වලට තුඩු දෙයි. මෙවැනි මිල අධික (සහ සැලසුම් නොකළ) නිෂ්පාදන වසා දැමීම්, පසුකාලීන ඇණවුම් සඳහා ද්රව්ය ඉවත් කිරීමේ අවශ්යතාවය සහ අඩුපාඩු නිවැරදි කිරීම සඳහා හදිසි කොටස් මිලදී ගැනීම් ඇති කරයි. ERP පද්ධතියේ වාර්තා නිෂ්පාදන තට්ටුවේ යථාර්ථය සමඟ අතින් සමමුහුර්ත කර ඇති අතර, නිෂ්පාදනය අත්යවශ්යයෙන්ම අත්හිටුවා ඇති විට, සාවද්ය කොටස් පාලනය මඟින් වෙබ් අඩවිය පුරා බඩු තොග විගණනය සඳහා කාලය ගතවන සහ මිල අධික භාවිතයට බල කරයි.
- අකාර්යක්ෂම රේඛා සැකසුම කාර්යක්ෂම SMT එකලස් කිරීමේ රේඛාවක් සිය ගණනක් සකසන විචල්යයන් එකවර සම්බන්ධීකරණය කිරීමේ හැකියාව මත රඳා පවතී. සකස් කරන ලද රේඛාවේ කිසියම් අංගයක් වැරදියි නම්, දුර්වල ගුණාත්මක ප්රතිදානය ප්රතිඵලයයි. මන්දගාමී රේඛා සැකසීම සහ නිදොස් කිරීම සඳහා පොදු හේතු කිහිපයක් තිබේ:
i. සැකසීමේ උපදෙස් යන්ත්ර වැඩසටහන් සමඟ නොගැලපේ - බොහෝ අවස්ථාවලදී, රේඛා වෙත පැමිණෙන ඉංජිනේරු දත්ත බහුවිධ, විසන්ධි වූ දත්ත ප්රවාහයන්ගෙන් පැමිණේ. එක් එක් යන්ත්රය සඳහා කට්ටල ලැයිස්තුව ERP පද්ධතියේ BOM වෙතින් ධාවනය වන නමුත් එය යන්ත්ර ක්රමලේඛකයින් විසින් ගන්නා ලද BOM-බෙදීම සහ තුලනය කිරීමේ තීරණ සැලකිල්ලට නොගනී. යන්ත්ර ක්රමලේඛ ජනනය කිරීම සඳහා භාවිතා කරන CAM පද්ධති බොහෝ විට ක්රියා කරන්නේ කර්මාන්තශාලා බිම සංචාරකයින් උත්පාදනය කිරීමට භාවිතා කරන CAM පද්ධතියට වඩා වෙනස් දත්ත ගබඩාවකිනි. තවද AOI යන්ත්ර ක්රමලේඛනය කිරීමට භාවිතා කරන CAM පද්ධති පික් සහ ස්ථාන යන්ත්ර ක්රමලේඛනය කිරීමට භාවිතා කරන පද්ධති වලට වඩා වෙනස් වේ. දත්ත ප්රවාහවල ඛණ්ඩනය විස්තීර්ණ විය හැක; ඉංජිනේරු දත්ත සමුදායන් අතර විසන්ධි වන සෑම ලක්ෂ්යයක්ම එකලස් කිරීමේ රේඛාවල විවිධ කොටස් සඳහා සමමුහුර්ත නොකළ දත්ත හෝ උපදෙස් උත්පාදනය කිරීමට තවත් අවස්ථාවක් ලබා දෙයි. සියලුම පිහිටුවීම් දෝෂ මූලාශ්රයේදී, සැලසුම අනුව ඉවත් කළ යුතුය, නැතහොත් “පළමු-ආෆ්ර” අදියරේදී සොයා ගත යුතු අතර රේඛාව පහත වැටී ඵලදායී නොවන විට සැකසීමේ උපදෙස් සංස්කරණය කිරීමෙන් ඉවත් කළ යුතුය.
ii. යන්ත්රවල කොටස්-දත්ත අස්ථානගත වී හෝ වැරදියි - සෑම SMT තේරීම් යන්ත්රයක්, AOI යන්ත්රයක් සහ පරිපත පරීක්ෂකයක් එක්රැස් කිරීමට, පරීක්ෂා කිරීමට හෝ පරීක්ෂා කිරීමට සෑම අංගයකම ප්රධාන ලක්ෂණ විස්තර කිරීමට දත්ත පුස්තකාලයක් අවශ්ය වේ. යන්ත්රයේ සංරචක පුස්තකාලය නිෂ්පාදන ඇණවුම සඳහා සංරචක විස්තර කරන දත්ත වලින් පුරවා ඇති විට පමණක් යන්ත්රයට එහි කාර්යය කළ හැකිය. කර්මාන්තශාලා බිමට පටවා ඇති සෑම නව කොටසක්ම අදහස් කරන්නේ එම කොටස සඳහා පුස්තකාල දත්ත යන්ත්ර තුළට ඇතුළු කර සත්යාපනය කළ යුතු බවයි. සාදන ලද පසු, සුදුසුකම් ලත් ක්රියාකරුවෙකු විසින් සිදු නොකළහොත් සිදු කරන ලද ඕනෑම වෙනස්කමක් අනවශ්ය කාලයකට හේතු විය හැකි බැවින් දත්ත නිසි ලෙස කළමනාකරණය කළ යුතුය. යන්ත්ර මට්ටමේ සංරචක දත්ත කළමනාකරණය කිරීම සඳහා පාලිත සහ මධ්යගත විසඳුමක් නොමැතිව, දත්ත යන්ත්ර කිහිපයක් තුළට ඉතා වෙහෙස මහන්සි වී ඇතුළු කළ යුතු අතර, එමඟින් අනවශ්ය අක්රීය කාලයක් සහ බහු යන්ත්ර අතර දත්ත අසමගිය වීමේ ඉහළ අවදානමක් ඇති කරයි.
iii. සම්පූර්ණ නොබැඳි සැකසුම සාක්ෂාත් කර නැත - බොහෝ නිෂ්පාදකයින්ට නොබැඳි සංරචක පැටවීමට සහ සත්යාපනය සැකසීමට හැකියාවක් නැත. මෙමගින් නිෂ්පාදන කටයුතු ආරම්භ කිරීමට ප්රථමයෙන් තීරු-පහළට රේඛා සහ සැකසීමට බල කෙරෙන අතර, නාස්තිකාර අක්රිය කාලයකට මග පාදයි. මාර්ගගතව සැකසීමෙන් සම්පූර්ණ පෝෂක ඉන්වෙන්ටරි පිරිවැය අවම කර ගත හැකි බවට සැකයක් නැත, නමුත් නැතිවූ රේඛා ප්රතිදානය සහ යන්ත්ර භාවිතය අනුව ඉහළ මිලක් ගෙවනු ලැබේ.
iv. පළමු-ඕෆ් අදියරේදී සැකසුම වැරදියි - ආරම්භයේ දී ඉන්වෙන්ටරි පරීක්ෂාවට සමාන්තරව සමස්ත පේළි සැකසීම සත්යාපනය නොකළේ නම්, පළමු-ඕෆ් නිෂ්පාදනය කරන අවස්ථාවේ දී දෝෂ හඳුනාගත යුතුය. දෝෂය නිර්මාණය කිරීම සහ අනාවරණය කිරීම අතර ගත වූ කාලය උපරිම වන බැවින්, සැකසීමේ දෝෂයක් සොයා ගැනීමට සහ ඉවත් කිරීමට වඩාත්ම මිල අධික ක්රමය මෙයයි. පෝෂක සංඛ්යාව, යන්ත්ර, වැඩසටහන් සංඛ්යාව අනුව දෝෂ/හඳුනාගැනීම/නිවැරදි අවස්ථා ගුණ කිරීම සහ සැකසීමේ නිදොස් කිරීමේ කාලය උත්සන්න කිරීමේ අවස්ථාව පැහැදිලි වේ, එය සිදු කරන විට පිහිටුවීමේ සෑම අංශයක්ම සත්යාපනය කිරීමට සාපේක්ෂව. පළමු අදියර සම්පූර්ණ වී රේඛාව සම්පූර්ණයෙන් නිෂ්පාදනය වූ පසු, අවසන් වූ පෝෂකයක් නැවත පිරවීම සඳහා යන්ත්රයක් මත නව කොටස් දැමූ විට දෝෂ මඟහරවා ගැනීම ද වැදගත් වේ. නරකම අවස්ථාවක, වැරදි ලෙස ස්ථානගත කර ඇති කොටස් සම්පූර්ණ කණ්ඩායම එකලස් කිරීමෙන් පසුව, පරීක්ෂා කිරීමේදී හෝ පරීක්ෂණ අදියරේදී අනාවරණය වේ. එවැනි අලුත්වැඩියාවන් උපරිම පිරිවැය සහ බලාගාරයේ සමස්ත ඵලදායිතාවයට බලපායි.
v. පවතින යන්ත්ර සැකසීම් ප්රයෝජනයට ගැනීමට අපොහොසත් වීම - සැකසීමේ අක්රිය කාලය අවම කිරීමට හොඳම ක්රමය නම් රේඛා ඉවත් කිරීමේ අවශ්යතාවය ඉවත් කර නිෂ්පාදන ඇණවුම් අතර ඒවා නැවත සැකසීමයි. අතිවිශාල විවිධ සංරචක, පෝෂක, පෝෂක ස්ථාන, සංරචක ප්රමාණයන් සහ අවම චක්ර කාලය සඳහා ප්රශස්ත සැකසුමකට බලපාන සාධක කළමනාකරණය කිරීමේ සංකීර්ණත්වය නිසා, බොහෝ නිෂ්පාදකයින් නිෂ්පාදන ඇණවුම් අතර රේඛා වලින් සියලුම පෝෂක සහ සංරචක ඉවත් කරයි. මෙය පාලනය පවත්වා ගෙන යන නමුත් ඵලදායිතාව නාටකාකාර ලෙස අඩු කරයි. නිෂ්පාදන ඇණවුම් කල්තියා විශ්ලේෂණය කිරීමෙන් සහ පිළිගත නොහැකි මට්ටමකට බීට් අනුපාතය කැප නොකර එකලස් කිරීමේ රේඛාවක එකම සැකසුම (හෝ සැකසීමෙන් බහුතරයක්) බෙදා ගත හැකි නිෂ්පාදන කණ්ඩායම් හඳුනා ගැනීමෙන්, අක්රීය කාලය තුළ විශාල ඉතිරියක් ලබා ගත හැකිය. නිෂ්පාදන-කණ්ඩායම් ශිල්පීය ක්රම භාවිතා කිරීම ඉහළ මිශ්රණය/අඩු-මධ්යම පරිමාවේ මෙහෙයුම්වල සැලකිය යුතු ඵලදායිතා වැඩිදියුණු කිරීම් ලබා දෙයි.
vi. අමතර කොටස් නැවත පිරවීමේ අවශ්යතා අපේක්ෂා කිරීමට අපොහොසත් වීම - ඉහළ පරිමා, අඩු මිශ්ර නිෂ්පාදන පරිසරයන් තුළ, සමස්තයක් ලෙස රේඛාව ක්රමලේඛනය කිරීම සඳහා නිවැරදි සමාකරණ-පාදක ප්රවේශයක් සඳහා අත්තිකාරම් නොමැතිකම. ii යන්ත්ර ක්රමලේඛනය සම්පූර්ණ චාලක අනුකරණය මත පදනම් නොවේ - රේඛීය මට්ටමේ අනුකරණය සහ ක්රමලේඛනය (සමතුලිත කිරීම) යන්ත්ර ක්රමලේඛනයෙන් වෙන් කළහොත්, දෙක අතර ගැටුමක් ඇති වේ; තුලනය තනි පුද්ගල චක්ර වේලාවන් පිළිබඳ නිවැරදි තොරතුරු මත රඳා පවතී, සහ යන්ත්ර ක්රමලේඛනය මඟින් රේඛීය තුලන ශ්රිතය මගින් උපකල්පනය කරන ලද වෙනස් යන්ත්ර චක්ර කාලයක් ජනනය කළ හැක. යතුර වන්නේ සෑම යන්ත්රයකම වින්යාසය (පෝෂක, තුණ්ඩ, …) සහ එහි චලන චාලකයේ ඉතා නිවැරදි අනුකරණයයි. යන්ත්ර චක්ර කාල අනුකරණයේ නිරවද්යතාවයකින් තොරව, තනි යන්ත්ර ක්රියාකාරීත්වය දුක් විඳීමට පමණක් නොව, ප්රශස්ත සමස්ත ප්රතිදානය සඳහා සමස්ත රේඛාව සමතුලිත නොවනු ඇත. රේඛාවේ කොටස් නැවත පිරවීමේ අවශ්යතාවයේ දෘශ්යතාව අක්රිය වීමට වඩාත්ම වැදගත් හේතුවයි. නරකම අවස්ථාව සිදු වන්නේ පෝෂකයක ඇති සියලුම සංරචක අවසන් වූ විට, නමුත් එය රේඛීය ක්රියාකරුට පුදුමයට කරුණක් වේ (ඒවාට පෝෂක සිය ගණනක් එකවර අධීක්ෂණය කිරීමට සිදු වේ). පෝෂකය ඉවත් කර, නව රීලයක් පටවන විට (එය අත ළඟ යැයි උපකල්පනය කර) සහ පෝෂක යන්ත්රය මතට නැවත පටවන විට මෙය රේඛාව පහළට බල කරයි.
- ප්රශස්ත ස්පන්දන අනුපාතවලට වඩා මන්දගාමී රේඛා සැකසූ පසු, නිෂ්පාදනය එහි පුනරාවර්තන රිද්මයට සමථයකට පත් වේ, රේඛීය ශේෂය, යන්ත්ර හැකියාවන් සහ නිෂ්පාදනයේ තැන්පත් කර ඇති ප්රශස්තිකරණ මට්ටම අනුව තීරණය වන ස්ථාවර සංඛ්යාතයකින් එකලස් කරන ලද PCB රේඛාවෙන් ඉවතට පැමිණේ. විශේෂිත යන්ත්ර වැඩසටහන් තමන්ම. මෙම අවස්ථාවෙහිදී, හැකි උපරිම තාල වේගයට රේඛා ක්රමලේඛනය කර නොමැති නම්, ඵලදායිතාව මිල අධික නමුත් නොපෙනෙන ආකාරයෙන් බලපායි. මෙය හේතු කිහිපයක් නිසා සිදුවිය හැක: i. සමාකරණය, BOM බෙදීම/ තුලනය කිරීම සහ යන්ත්ර ක්රමලේඛනය සම්පූර්ණ රේඛා මට්ටමින් සිදු නොකෙරේ - තනි යන්ත්ර ප්රශස්ත මට්ටමකට ක්රමලේඛනය කළ හැක, නමුත් සම්පූර්ණ චාලක අනුකරණයක් මත පදනම්ව ක්රමලේඛන කාර්යයට සම්පූර්ණ රේඛා ප්රවේශයක් නොගතහොත් රේඛාව සෑදී ඇති සියලුම යන්ත්රවලින්, සමස්ත කාර්ය සාධනය දුක් විඳියි, මූලික වශයෙන් යන්ත්ර වැඩ බර අසමතුලිතතාවය නිසා සිදු වේ. රේඛාවේ චක්ර කාලය හෝ බීට් අනුපාතය තීරණය කරනු ලබන්නේ රේඛාවේ ඇති මන්දගාමීම යන්ත්රය මගිනි, සමස්තයක් ලෙස රේඛාව ක්රමලේඛනය කිරීම සඳහා නිවැරදි සමාකරණ-පාදක ප්රවේශයක් අවශ්ය බව අවධාරණය කරයි.
ii. යන්ත්ර ක්රමලේඛනය සම්පූර්ණ චාලක අනුකරණය මත පදනම් නොවේ - රේඛීය මට්ටමේ අනුකරණය සහ ක්රමලේඛනය (සමතුලිත කිරීම) යන්ත්ර ක්රමලේඛනයෙන් වෙන් කළහොත්, දෙක අතර ගැටුමක් ඇති වේ; තුලනය තනි පුද්ගල චක්ර වේලාවන් පිළිබඳ නිවැරදි තොරතුරු මත රඳා පවතී, සහ යන්ත්ර ක්රමලේඛනය මඟින් රේඛීය තුලන ශ්රිතය මගින් උපකල්පනය කරන ලද වෙනස් යන්ත්ර චක්ර කාලයක් ජනනය කළ හැක. යතුර වන්නේ සෑම යන්ත්රයකම වින්යාසය (පෝෂක, තුණ්ඩ, …) සහ එහි චලන චාලකයේ ඉතා නිවැරදි අනුකරණයයි. යන්ත්ර චක්ර කාල අනුකරණයේ නිරවද්යතාවයකින් තොරව, තනි යන්ත්ර ක්රියාකාරීත්වය දුක් විඳීමට පමණක් නොව, ප්රශස්ත සමස්ත ප්රතිදානය සඳහා සමස්ත රේඛාව සමතුලිත නොවනු ඇත.
iii. යන්ත්ර මට්ටමේ කොටස් දත්ත ප්රශස්ත ලෙස හැසිරවීමේ කාර්ය සාධනය සඳහා ක්රමලේඛනය කර නොමැත - එක් එක් යන්ත්රය විසින් භාවිතා කරන කොටස්-දත්ත මඟින් සංරචක හැසිරවිය යුතු ආකාරය නිර්වචනය කරයි: කුමන වේගයකින්, කුමන තුණ්ඩය සමඟද, විවිධ වාසස්ථාන කොපමණ කාලයක් පැවතිය යුතුද, කුමන ඕෆ්සෙට් යෙදිය යුතුද? පිකප් පොයින්ට් එක සහ යනාදිය. නිෂ්පාදිතය නිවැරදිව එකලස් කර ඇති බව තහවුරු කර ගැනීමට පළමු-ඕෆ් සම්පූර්ණ කිරීම ප්රමාණවත් වේ, නමුත් මෙය යන්ත්රයේ කොටස් දත්ත පුස්තකාලයට ඇතුළත් කර ඇති උප-ප්රශස්ත හැසිරවීමේ උපදෙස් හේතුවෙන් අඩු එකලස් කිරීමේ වේගයක් නිරාවරණය නොකරයි. ක්රියාකරුවෙකු සමහර විට එකලස් කිරීම සහතික කිරීම සඳහා සංරචකයක ස්ථානගත කිරීමේ වේගය අඩු කිරීමට තෝරා ගනු ඇත, බොහෝ විට නඩත්තු ගැටළු ආවරණය කරමින් රේඛාවේ සමස්ත ඵලදායිතාව විශාල ලෙස අඩු කරන අතරම විසඳිය යුතුය. යන්ත්ර ක්රමලේඛවල ප්රශස්තකරණය මෙන්ම, සවිස්තරාත්මක කාර්ය සාධන දත්ත වෙත ප්රවේශ වීමකින් තොරව මිනිසුන්ට මෙම බලපෑම් හඳුනාගැනීම පාහේ කළ නොහැක්කකි; සහ හඳුනාගැනීමකින් තොරව ඒවා නිවැරදි කළ නොහැක.
- අඩු යන්ත්ර උපරිම කාර්ය සාධනය ඩොලර් මිලියන ගණනක් දක්වා දිවෙන රේඛාවල ආයෝජන සමඟින්, පැහැදිලිවම යන්ත්ර උපරිම කාලය සඳහා උපරිම ඵලදායිතාවයකින් ක්රියා කිරීමට නඩත්තු කළ යුතුය. කෙසේ වෙතත්, සමස්ත කාර්ය සාධනය පහත හෙලීමට ද්රෝහී බලපෑමක් ඇති යන්ත්ර තත්වයේ බොහෝ අංග තිබේ.
- තුණ්ඩ රික්ත පීඩනය - මෙය පිරිවිතරයෙන් බැහැර නම්, එය පික්-අප් ලක්ෂ්යය සහ PCB මත ඒවායේ පිහිටීම අතර සංක්රමණයේදී සංරචක පහත වැටීමට හේතු වේ.
- ඇලෙන සුළු තුණ්ඩ රික්ත මාරු කිරීම - රික්ත ස්විචය ඇලෙන සුළු නම් එය තුණ්ඩ ස්කිප් වලට යොමු කරයි. දෝෂයකින් තොරව පෝෂකයෙන් සංරචක තෝරා ගැනීම සඳහා තුණ්ඩ වෙත රික්ත සැපයුම ධනාත්මක හා වේගයෙන් මාරු කිරීම අවශ්ය වේ. ස්ථානගත කිරීම සඳහා ද එය අදාළ වේ; රික්තය සෙමින් හෝ අපැහැදිලි ලෙස මාරු කිරීම නිරවද්ය ලෙස ලබා ගැනීමට හෝ ස්ථානගත කිරීමට හේතු වේ.
- වර්න් ෆීඩර් - මෙය ඉහළ මිස් පික් අනුපාතවලට මග පාදයි. සංරචක පෝෂක යනු කාලයත් සමඟ අඳින යාන්ත්රික සුචිගත කිරීමේ උපාංග වේ. යාන්ත්රණය සාමාන්ය භාවිතයෙන් අඳින විට, පිකප් සඳහා සංරචකය ඉදිරිපත් කිරීමේ නිරවද්යතාවය අඩු වන අතර, නිවැරදිව තෝරා ගැනීමට අසමත් වීමට හේතු වන අතර එමඟින් සංරචක සහ චක්ර කාලය නාස්ති වේ. iv. දුර්වල නඩත්තු උපදෙස් - SMT රේඛා පැයකට කොටස් දස හෝ සිය දහස් ගණනින් කොටස් ස්ථානගත කරයි. මෙම අකුණු යන්ත්ර වේගය අඩුවන ක්රියාකාරීත්වය නිරීක්ෂණය කිරීම අපහසු කරයි. මිස්-පික්ස් දැකීමට නොහැකි තරම් ඉක්මනින් සිදු වේ, නමුත් පුනරාවර්තන ශ්රිතයක මිලි තත්පර කිහිපයක ප්රමාදයක් කාර්ය සාධනය අඩු කිරීමට හේතු වේ. කාර්ය සාධනය පහත වැටීම් කොතැනද යන්න පිළිබඳව නිවැරදි සහ කාලෝචිත දැනුම්දීමකින් තොරව, රේඛීය ක්රියාකරුවන්ට සහ නඩත්තු සේවකයින්ට කාර්ය සාධනය ඉහළ නැංවීමට නිවැරදි ක්රියාමාර්ග ගැනීමට ඇති ඉඩකඩ අඩුය.
- දුර්වල නඩත්තු උපදෙස් - SMT රේඛා පැයකට කොටස් දස හෝ සිය දහස් ගණනින් කොටස් ස්ථානගත කරයි. මෙම අකුණු යන්ත්ර වේගය අඩුවන ක්රියාකාරීත්වය නිරීක්ෂණය කිරීම අපහසු කරයි. මිස්-පික්ස් දැකීමට නොහැකි තරම් ඉක්මනින් සිදු වේ, නමුත් පුනරාවර්තන ශ්රිතයක මිලි තත්පර කිහිපයක ප්රමාදයක් කාර්ය සාධනය අඩු කිරීමට හේතු වේ. කාර්ය සාධනය පහත වැටීම් කොතැනද යන්න පිළිබඳව නිවැරදි සහ කාලෝචිත දැනුම්දීමකින් තොරව, රේඛීය ක්රියාකරුවන්ට සහ නඩත්තු සේවකයින්ට කාර්ය සාධනය ඉහළ නැංවීමට නිවැරදි ක්රියාමාර්ග ගැනීමට ඇති ඉඩකඩ අඩුය.
- අකුණු මැෂින් වේගය අඩු වන කාර්ය සාධනය නිරීක්ෂණය කිරීම අපහසු කරයි. මිස්-පික්ස් දැකීමට නොහැකි තරම් ඉක්මනින් සිදු වේ, නමුත් පුනරාවර්තන ශ්රිතයක මිලි තත්පර කිහිපයක ප්රමාදයක් කාර්ය සාධනය අඩු කිරීමට හේතු වේ. කාර්ය සාධනය පහත වැටීම් කොතැනද යන්න පිළිබඳව නිවැරදි සහ කාලෝචිත දැනුම්දීමකින් තොරව, රේඛීය ක්රියාකරුවන්ට සහ නඩත්තු සේවකයින්ට කාර්ය සාධනය ඉහළ නැංවීමට නිවැරදි ක්රියාමාර්ග ගැනීමට ඇති ඉඩකඩ අඩුය.
- PCB/ක්රියාවලි සංයෝජනය උප-ප්රශස්ත PCB එකලස් කිරීමේ ක්රියාවලි හිතකාමී හෝ ක්රියාවලි-සතුරු ලෙස සැලසුම් කළ හැක. බොහෝ PCBs අවසානයේ එකලස් කළ හැක, නමුත් උප-ප්රශස්ත නිර්මාණය, ප්රතිනිර්මාණය කිරීමේ මට්ටම් සහ රේඛීය කාර්යක්ෂමතාව හේතුවෙන් අවශ්ය ප්රමාණයට වඩා වැඩි පිරිවැයක් වැනි සැලසුම් විශේෂාංගවල ප්රතිඵලයක් ලෙස වෙනස් වේ:
i. PCB යන්ත්ර හෝ රේඛීය හිතකාමී නොවේ - විශ්වාසයන් සැඟවී ඇත, සංරචක වාහක සමඟ ගැටේ, එකලස් කිරීමේ-පැනල් සැලසුම ප්රශස්තකරණයට හිතකර නොවේ. පුවරුවේ ඇති සංරචක බෙදා හැරීම, හෝ BOM මත විවිධත්වය වැනි සැලසුම් සීමා කිරීම්, එක් යන්ත්රයකට අඩු ස්ථානගත කිරීමේ පිරිවැයක් ලබා ගත නොහැකි වන අතර නිෂ්පාදිතය රේඛාව මත ධාවනය වන තෙක් මෙය දෘශ්යමාන නොවේ.
ii. Solder-stencil නිර්මාණය උප-ප්රශස්ත සොල්දාදු සන්ධි වලට මග පාදයි - මෙය ඉහළ ප්රතිනිර්මාණයක් ඇති කරයි. එකලස් කිරීමේ මූලික පරමාර්ථය වන්නේ විශ්වසනීය පෑස්සුම්-සන්ධි නිර්මාණය කිරීමයි. පෑස්සුම් ක්රියාවලිය පිළිබඳ හොඳ පාලනයකට අමතරව, පිළිගත හැකි ඉවසීම් තුළ (සාමාන්යයෙන් දුර්වල සන්ධි දස ගණනකින් මනිනු ලබන) සන්ධි සාක්ෂාත් කර ගැනීමේ හොඳම අවස්ථාව ක්රියාවලියට ලබා දීම සඳහා සංරචක පින්, පෑඩ්-රටාව සහ පෑස්සුම්-ස්ටෙන්සිල් විවරය ප්රශස්ත කළ යුතුය. නිෂ්පාදනය මිලියනයකට).
iii. PCB සැලසුම් පිරිසැලසුම දුන්න සහ කරකැවීම දිරිමත් කරයි - එකලස් කිරීම සඳහා රේඛාවට පටවා ඇති PCB වල පැනල සම්පූර්ණයෙන්ම සමතලා විය යුතුය, එවිට යන්ත්රවල වාහක “එල්ලීම” සහ සැකසුම් දෝෂ වළක්වා ගත යුතුය. සියලුම අක්ෂවල තඹ ඒකාකාර ව්යාප්තියකින් PCB නිර්මාණය කිරීමෙන්, සැකසීමේදී PCB නැමීමට සහ ඇඹරීමට ඇති ප්රවණතාවය අවම වේ.
iv. පෑඩ්/ට්රැක් රටා නැවත ප්රවාහයේදී සොහොන් ගල් තැබීම දිරිමත් කරයි - දැන් පරිමාවෙන් හසුරුවන 0201 පැකේජ වැනි කුඩා නිෂ්ක්රීය චිප්-සංරචක වෙත නැඹුරු වීමත් සමඟ, සංරචකයේ දෙපස සමාන තාප ගිල්වීමේ බලපෑම්වලට ඉඩ සැලසෙන පරිදි පෑඩ් සහ ධාවන රටා සැලසුම් කිරීම වැඩිවන වැදගත්කමකින්. සංරචක සැහැල්ලු වන විට, නැවත ගලා යාමේදී මතුපිට ආතති බලපෑම්වල බලපෑම වඩාත් වැදගත් වේ; එක් පැත්තක් අනෙක් පැත්තට පෙර නැවත ගලා ගියහොත්, පෘෂ්ඨික ආතතිය සන්ධියේ වියළි පැත්ත එසවීමට හේතු විය හැක, එය "සොහොන් ගල" බලපෑම ඇති කරයි.
සමහර විසඳුම්
කර්මාන්තශාලා බිම්වල ඵලදායිතාව උපරිම කිරීම සඳහා මාර්ගය පිහිටා ඇත්තේ පෙර කොටස්වල සවිස්තරාත්මක මෙහෙයුම් කරුණු ආමන්ත්රණය කරන ඉහළ-පහළ ප්රවේශයකිනි. පහත සඳහන් ක්ෂේත්රවල පියවර ගත යුතුය: දත්ත සැකසීම නිෂ්පාදන ක්රියාවලි අනුකරණය නිෂ්පාදන ක්රියාවලි සකස් කිරීම නිෂ්පාදන ක්රියාත්මක කිරීමේ පද්ධති මෙම සියලු අභියෝග සඳහා තාක්ෂණික විසඳුම් අවශ්ය වේ. තවද, තීරණාත්මක ලෙස, කාර්ය සාධනය වැඩි දියුණු කිරීම සඳහා ගත යුතු නිශ්චිත ක්රියාමාර්ග හඳුනා ගන්නා ඉංජිනේරුවන්, රේඛීය ක්රියාකරුවන් සහ නිෂ්පාදන කළමනාකරුවන් සඳහා වාර්තාකරණ පද්ධති ක්රියාත්මක විය යුතුය. එපමනක් නොව, අවස්ථාව අහිමි වීමට පෙර සහ වෙනත් තැන්වල නැවුම් ගැටළු මතු වීමට පෙර වැඩිදියුණු කිරීම් සිදු කිරීමට හැකි වන පරිදි තොරතුරු කාලෝචිත විය යුතුය. දත්ත සැකසීම සංරචක ආකෘති ආදානය සහ සැලසුම් දත්ත ආදානය යන දෙකටම දත්ත සැකසීම කෙරෙහි අවධානය යොමු කිරීම අනිවාර්ය පළමු පියවරකි: සංරචක ආකෘති නිර්මාණය - නිෂ්පාදකයින් විසින් පෑස්සුම් සඳහා සම්බන්ධතා සම්බන්ධතා ඇතුළුව රේඛාවේ භාවිතා කිරීමට අදහස් කරන සියලුම කොටස්වල නිවැරදි භෞතික ආකෘති නිර්මාණය කළ යුතුය. සන්ධි, CAD දත්ත සමඟ ඒකාබද්ධ වේ. මෙය සමන්විත විය යුතුය: ස්ථාවර, CAD-පුස්තකාල මධ්යස්ථ, ප්රමිතිගත DFM සහ ක්රියාවලි සැකසීමේ ක්රියාකාරකම් පහළට සක්රීය කිරීම සඳහා කොටස් ආකෘතිකරණය. සාමාන්යකරණය කරන ලද සංරචක ඕෆ්-සෙට්, භ්රමණ සහ ධ්රැවීයතා ප්රකාශ ප්රමිතියකට.
අදහස් කිසිදු